As a professional buyer of packaging materials, the ability to balance and control the inventory of packaging materials determines the business level of their supply chain management. Inventory comes from the production plan of brand products, and also from an estimate of the brand market. Inventory is not only the accumulation of costs but also a buffer zone to support the rapid response of the market. We briefly analyze how to effectively manage and control the inventory of packaging materials in this article. The content is only for the reference:
- Establish a clear classification system for packaging materials:
- Classify packaging materials according to different types, sizes, materials, and other factors, and set a unique identification code for each category.
- Identify packaging materials using technologies such as electronic tags, barcodes, or RFID, so that specific packaging materials can be easily tracked and found in the inventory management system.
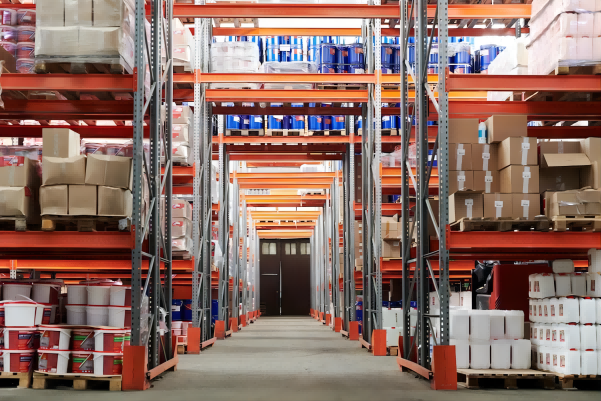
2. Implement advanced packaging material inventory management system:
- Choose an inventory management software or system suitable for the size and needs of the enterprise, so as to realize real-time recording, tracking, and management of inventory data.
- Establish a complete list of packaging materials in the system, including packaging material names, specifications, purchase prices, supplier information, etc., for quick search and management.
3. Set optimal packaging stock levels:
- Set a reasonable optimal inventory level based on factors such as the frequency of use of packaging materials, supply cycle, and sales forecast.
- Conduct inventory optimization analysis, consider factors such as inventory cost, order delivery time, and sales demand fluctuations, and formulate inventory management strategies.
4. Establish a warning line for packaging material inventory:
- Set inventory warning lines based on historical demand and supplier delivery time.
- Once the inventory is lower than the warning line, the ordering or purchasing process will be triggered, and enough time will be reserved before purchasing to ensure that the supply of packaging materials can meet production needs.
5. Implement advanced forecasting and demand planning techniques:
- Use data analysis tools and market trend forecasting techniques to help you forecast packaging material needs more accurately.
- Combining information such as historical sales data, new product launch plans, market trends, and promotional activities, to formulate a reasonable packaging material procurement plan.
6. Inventory rotation and FIFO principle:
- For the same type of packaging materials, make sure to use the packaging materials that have been stored for a long time first to follow the first-in-first-out principle.
- Implement automated stock rotation functionality in the inventory management system to avoid expiry, quality degradation, and wastage of packaging.
7. Regular inventory and adjustment of packaging material inventory:
- Regularly conduct an inventory of packaging materials to verify the accuracy of inventory and recorded data. Make sure the physical inventory is consistent with the data in the system.
- Upon discovery of any inventory discrepancy or loss, promptly adjust records and investigate the cause to prevent similar situations from happening again.
8. Collaborate with suppliers and other departments:
- Work with suppliers: Work with suppliers to jointly assess the efficiency and reliability of the supply chain. Discuss possible options for improving the supply chain, such as reducing lead times, improving order accuracy, sharing sales data and demand forecasting, and more. Continue to communicate with suppliers and establish a close cooperative relationship to better meet the needs of the company.
- Work closely with sales and production teams to share timely information such as sales forecast data, new product plans, and promotional activities in order to adjust packaging material procurement plans.
9. Optimizing supply chain and logistics:
- Research opportunities to optimize supply chain management and logistics distribution to reduce procurement costs and increase speed and accuracy of delivery.
- Explore cooperation with reliable suppliers to optimize supply chain processes, such as adopting the Just-in-Time mode to reduce inventory backlog and transportation costs.
10. Implement periodic review and improvement:
- In order to optimize packaging material inventory management, it is crucial to implement regular reviews and improvements. Here are more detailed steps:
- Review inventory data: Regularly review packaging material inventory data, including inventory levels, inventory turnover, inventory accuracy, etc. Analyzing this data can help you understand inventory management performance and spot anomalies or irregularities.
- Analyze Inventory Variances: Compare actual inventory with system-recorded inventory data to find and analyze any inventory discrepancies. These discrepancies may be due to recording errors, loss, theft, damage, or other uncertainties. By understanding the cause of variance, you can take corrective action and improve the accuracy of inventory management.
- Develop an improvement plan: According to the results of the review and analysis, develop an improvement plan to solve existing problems and bottlenecks. This may involve updating or replacing inventory management systems, improving employee training, adding inspection procedures and standard operating procedures, and more.
11. Maintain environmental hygiene:
- Regularly clean and organize the packaging material warehouse to ensure that the packaging materials are stored in a clean, tidy, and dust-free environment.
- Use appropriate storage equipment and containers to ensure the safety of packaging materials and prevent damage or contamination, such as using shelving, protective sleeves, etc.
12. Train warehouse staff:
- Train warehouse staff to familiarize them with the packaging material inventory management system and operating procedures.
- Cultivate the sense of responsibility and professional skills of employees, so that they can accurately record and process the information of packaging materials entering and leaving the warehouse.
- Continuously train and improve the inventory management skills of employees so that they can better understand and adapt to the latest inventory management methods and tools.
13. Regularly review packaging material suppliers:
- Regularly review the performance of packaging material suppliers, including supply stability, product quality, and delivery time accuracy.
- Conduct supplier performance evaluations on suppliers to identify problems and take necessary corrective actions in a timely manner.
14. Control procurement costs:
- Regularly evaluate the price competitiveness, product quality, and service level of different suppliers to ensure the most valuable packaging materials.
- Negotiate and negotiate with suppliers for better prices and contract terms.
- Plan purchase batches and avoid over-purchasing to reduce inventory backlog and storage costs.
15. Risk management:
- Understand the risks in the packaging material market and supply chain, and formulate corresponding coping strategies. For example, establishing backup suppliers to cover the risk of supply chain disruptions.
- Find alternative material and packaging options to allow flexibility in case of supply issues or price fluctuations.
16. Data analysis and continuous improvement:
- Use data analysis tools and reports to track key indicators (such as turnover rate, inventory accuracy rate, etc.) to evaluate the performance of packaging material inventory management.
- Based on the data analysis results, identify potential improvement opportunities and formulate corresponding improvement plans.
- Regularly hold review meetings with relevant departments to share and discuss experiences and best practices on packaging material inventory management.
Summary:
Through meticulous packaging material inventory management, you can accurately grasp the actual inventory situation, avoid inventory shortages and excesses, reduce storage costs, and improve production efficiency and customer satisfaction. Stay vigilant at all times, adapting strategies and processes to adapt to changing market demands and supply chain environments.